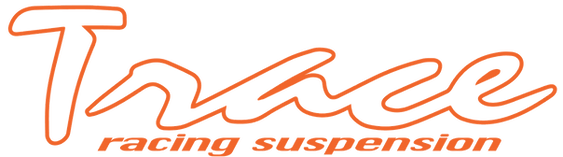
MBR メイクバンプラバーの開発について。
私には物造りの師が御二人います。御一人は、OS技研の創設者で有る、岡崎氏。
もう一人は、エンドレスの創設者で有る、亡き、花里氏です。
御二人からの共通の教えは、「無い物は造れ」この一言でした。
MBRの開発を初めて2年、まだまだ完璧な物では有りませんが、一つの区切りとして販売を開始させて頂ます。今後の開発も、二人の師に習い、残りの人生を掛けて行います。
MBRの必要性
レースシーンでのサスペイション開発を初めて、三十数年。
数多くの車輛セットアップを始め、商品開発に携わるチャンスを与えて頂けた事が、今の私を育んでいると感謝しています。
レースシーンでのサスペイションの働きは、タイヤをグリップさせる事と思われがちですが、グリップを生むだけではタイムには繋がりません。程よいグリップ力とコントロール性がタイムに繋がると言うのが、私の自論です。
では、タイヤをそのように使う為には何が必要なのか。それが、私の課題でした。
タイヤは開発されてから100年あまりたちますが、見た目的にも、素材的にも大きな変化は有りません。素材は天然ゴム製で、中に空気が入り、適度な摩耗性の有る物です。
構造的な進歩や、材質的な進歩が有るため、摩擦係数は向上し、結果的には耐荷重の高い物へ進歩はしています。
サスペイションを観た場合も、車が開発されてから100年あまり経過はしていますが、構造的な変化はそれほど大きく無く、荷重を受け止めるバネと、バネの収束を補う減衰装置で構成されています。こちらも当然ながら材質的な進歩や、減衰装置の改善により、耐荷重の高い物として進歩はしています。
タイヤは回転しながら路面を転がり、路面への接地面によりグリップが発生します。
回転により路面に対して接地する部分が絶えず変成・復元・を繰り返すため、タイヤには変化する振動が発生します。その複雑な振動に対して、面圧を掛けるため、バネの反発力を利用します。バネの反発はその収束性が低いため、減衰装置により収束を補います。これが大きく考えた場合のサスペイションの動きと成ります。しかし実際は、ゴムで出来ているタイヤには自らの反発力と収束性を持ち合わせ、その変成・復元にヒステリシスが存在するため、振動にラグが発生する物と成ります。つまり、振動を周期的な物と捉えた場合、その速度にズレが有る物で尚且つ、その周期も一定では無い物に対しての面圧を掛ける物が必要と言う事に成ります。
つまり、タイヤとサスペイションの関係は、各々の異なる周期速度に対しての同調性や非同調性を組み合わせる事により、その場その場において、必要とされるグリップを生み出す物と言う事になる訳です。
これを、周期速度の同調性から観た場合、周期速度の速いタイヤに対してのグリップ力は周期速度の速いサスペイションが優位となり、非同調性で考えればそのヒステリシスが大きな物が優位と成ります。つまり、タイヤの構造が硬く、ハイグリップ化された、耐荷重の高いタイヤに対しては、高レートスプリングの速い周期速度を利用し、その周期速度に見合う減衰レスポンスが必要と言う事に成ります。
コントロール性の観点からすると、タイヤの周期速度を超える速度を持たせた、高レートに依存する事でも、逆に逸脱する速度の遅さを持つ、低レートでも可能と成ります。
減衰特性も同じで、過剰なヒステリシスでも、小さすぎるヒステリシスでも可能です。
また、レート依存に対しての周期速度の考え方にも、多様性が存在します。
コイルスプリングの周期速度は実際にそれを測定する事は不可能な物で、通常は固有振動数と言う括りが存在します。これも私的な自論に成りますが、コイルスプリングにおける周期速度は、造り出されたレートの中に存在する物では無く、線材の中に、「線材の太さ」、「線材の硬さ」、の融合物として、製造段階の形状記憶の中に埋め込まれた存在で有る。と
それを使い、巻き数の違いにより造り出されたレートには、その線長により周期速度のズレとなるヒステリシスが存在する物で有り、振動数とは異なる物と成ります。
また、減衰装置となるダンパーにも、速度を収束させる減衰特性が有り、周期速度への同調性と非同調性が存在します。元々、減衰特性はヒステリシスの塊と言って問題有りませんが、実際に発生する減衰はその速度域により、異なる手法で取り出す物のため、その造り方により、ヒステリシスのズレが存在します。ただ、このズレに対しての測定もその測定にヒスゲージを用いるため、実際の「振動」に対しての測定では有りません。
結果、この大きく分類して3種類になる、「タイヤ」・「スプリング」・「タンパー」・の構築において、その周期速度を、前後4輪のタイヤに対して、コントロールする事が、サスペイションエンジニアの仕事となる訳ですが。
サスペイションは、タイヤをグリップコントロールするための構築材ですが、タイヤとは全く異なる物質で出来ています。
スプリングは、大きな耐荷重を持たせるために「鉄」が基本です。
減衰を発生させるダンパーには流動抵抗体となる「オイル」が主で、そのオイルを遮断し、減衰レスポンスを発生させるためのシムも「鉄」が使われています。
タイヤとは、全く異なる物性値を持つ物で、その周期速度の同調性と非同調性を求める事になるわけで、どちらかと言うと非同調性に準じていると考えられます。これはブレーキと類似しますが。
つまり、これを現在の車輛に取り入れた場合、周期速度の同調性の観点から、何らかの同調性を持つ構築材を補足する事が望ましいと言う結論に成ります。これがバンプラバーの純正採用を促している訳ですが、実はもう一つの理由が存在します。
それが、最近の車輛に搭載されている安全ABS装置(横滑り防止装置)の義務化です。
これをサーキット等、スポーツ走行で、過剰に作動させた場合、問題が起こります。
従来のABSシステムを進化させたVDC等は、横滑り(スリップ率)を感知するため、車輪速から求める推定車速が重要となります。そのため、後輪に対してフリーの時間(増圧されない時間)が大幅に増加し、後輪に対してのブレーキが効かない状態が長く続きます。
粗、「前輪だけで止めている」と、言っても過言では有りません。
これを、前後輪の制動で考えた場合、前輪制動に対しては、同調性の演出に対し、高レート化や低速減衰で有る程度は対応可能ですが、制動が無いため、受け身と成る後輪に対しては、同調性が難しいのが現状と成ります。
これらの理由から、比較的に安易な手法となる、バンプラバーが登場する事に成ります。
純正採用品を始め、多くの社外品のバンプラバーに関して、ウレタン製の普及が一般的です。ウレタンの特長として、形状的に自由度が高く、製作コストも低く、レート(耐荷重)の設定も比較的容易です。
私も以前は、ウレタン製を多用していましたが、、レースシーンで使用した場合、解決出来ない難点が一つ存在しました。
それが、タイヤに対して作用する、縦横グリップ比率です。(特に後輪に対して)
これも、私の自論に成りますが、タイヤには横方向に対してのグリップと、縦方向に対してのグリップを求められます。これを維持する作用が、ヒステリシスに成ります。
各々のヒステリシス(タイヤ・スプリング・減衰・に存在する)は、その作用させる時間(周期)が有り、それをラグ(周期のズレ)として捉えます。横方向のグリップ作用はこれを多く求められます。逆に、ヒステリシスからの復元となる作用が、縦方向のグリップに作用します。
これを、伸縮の動きとして簡単に説明すると、縮む方向の周期に対して、ラグを使うと横方向のグリップが発生し易く、伸びる方向の周期に同期させると、縦方向のグリップが発生し易いと言う事に成ります。
これを、タイヤのコーナリングフォームで考えた場合、前輪タイヤに対しては、縦変成から横変成に移り、元の形状に戻って行きます。 後輪は、横変成から縦変成に移り、元の形状に復元する事に成ります。つまり、前後輪では、変成の順序が逆な訳です。
ここに、ウレタン製のバンプラバーを後輪に対して使用した場合、受け止める荷重に対しての能力は有るが、スプリングのように、それを返す能力が無い、と言う特性が難点と成ります。
つまり、ヒステリシスと、タイヤの変成・復元・のバランスを融合させる場合、後輪に対して復元要素が欠落しているという結論になり、「トラクションを生みにくい」と言う結果に成ります。
これらの条件や状態を加味した上で、理想のバンプラバーを考案した場合、次に上げる条件が必要に成ります。
① タイヤの高荷重化に対して、周期速度の同調性を高める性能を有する物
② 増加傾向に有る車輛重量に対して、耐荷重を有し、又、反発を有する物
➂ 安全ABSの義務化に対して、有効な能力を有する物
④ 前後輪に対して、定数・反発(周期速度)の違いを有する物
⑤ レバー比率により、異なる荷重に対して、組合わせる能力を有する物
これらが、MBRを開発する目標と成りました。
以上の条件を満たす課題としては、以下の選択が必要でした。
① 材質の選択 (既存の材質を使用する)
② 形状の選択 (球体形状・樽型形状・円柱形状を使用する)
➂ 作動量の選択 (体積により作動量を確保する)
④ 組み合わせの選択 (縦列積層をし易い形状にする)
⑤ 適応荷重の選択 (使用出来る作動量を明確にする)
開発での問題と注意点
① 直圧加熱成形による、温度と加硫時間の管理(定数とヒステリシスの変化)
② 色付けに用いるシリカとカーボンによる性能の違い(定数とヒステリシスの変化)
➂ 縦列積層の方法(スペーサーの必要性・材質の違い)
④ 硬度とホール形状のバランス
⑤ 実測レートと使用感の違い
⑥ 硬度と体積のバランスによるヒステリシスの存在(テスト中)
結果、構想から2年半、12種類の形状、3種類の硬度で 36種類の製品に成りました。
これが、MBRに求められる全てでは無いと思いますが、現状、許容荷重・許容ストローク・ヒステリシスのバランスを融合出来るまでの製品には成っています。
また、今後も、改良・改善・を含め、進化させ続けます。
2022年12月末、体調が悪化していた花里会長から連絡が有り、2023年の東京オートサロンでMBRを発表するように言われました。
まだ開発途中で有る事を伝えましたが。
「それで良いんだよ。」て。
今思えば、花里会長からの、最後の宿題、だったと思います。
「会長、お疲れ様でした。 会長に笑われないように、残りの人生を歩みます。」
「有難う御座いました。」
「MBR、形になったヨ。」
渡海 正雄
